Home | Grundfos | Case Studies | At Scottish Sea Farms salmon hatchery thrives with reliable pumps
At Scottish Sea Farms salmon hatchery thrives with reliable pumps
Scottish Sea Farms wanted more control and higher survival rates in
its salmon – from egg to adult. And it wanted a more sustainable system.

Two fish tanks for young smolt salmon in Scottish Sea Farms’ Barcaldine hatchery.
Scottish Sea Farms wanted more control and higher survival rates in its salmon – from egg to adult. And it wanted a more sustainable system.
The company thus built a recirculating aquaculture system (RAS) at its Barcaldine (UK) hatchery, reusing 96% of the water.
More than 250 Grundfos pumps move the water and fish between tanks, as well as moving the water back through the RAS system, including mechanical filtration, temperature control, disinfection and other applications.
A sudden pump failure would be catastrophic for the plant. Since the plant was put into full operation in 2019 the pumps have run without any major breakdowns.
The Situation
Scottish Sea Farms – a land-and marine-based salmon farmer – used to operate its hatcheries with the “flow-through” water technique. They brought fresh water into their plants from nearby rivers or lakes, let it flow through their tanks and systems and then flow out again, back to the original water sources.
This method posed a challenge, however. There was little control over what nature gives you.
“You can’t control the temperature, you can’t control the water quality very well,” says Ewen Leslie, Freshwater Engineering Manager at Scottish Sea Farms Barcaldine hatchery. For instance, inside the hatchery, the water must be 12°C (54°F). But incoming water temps in Scotland can swing wildly, depending on the season – as low as 2°C or as high as 20°C. The hatchery must thus spend a lot of resources heating or cooling the water. And that’s only one challenge – among several others relating to having control over a system that was increasingly unsustainable on different levels. Swinging temperatures and other factors also have the potential to stress the salmon, affecting growth.
You can't control the temperature, you can't control the water quality very well.
Ewen Leslie, Freshwater Engineering Manager at Scottish Sea Farms

The Scottish Sea Farms Barcaldine hatchery in the Scottish Highlands near Oban, UK.
Reducing water use by 100x
Around the time the company was planning a new hatchery in Barcaldine in the Scottish Highlands in the mid-2010s, a new technology had matured, called recirculating aquaculture system [RAS].
“Recirculation means you’re recycling 96% of the water,” Ewen Leslie says. “Therefore, the energy you’re putting into it, you’re reusing it, you’re not wasting it at all.”
Denmark-based RAS system builder Billund Aquaculture built the plant in 2017. It was in full production by 2019. Billund Aquaculture’s Chief of Sales, Bjarne Hald Olsen, explains that flow-through systems use 50,000 litres of water to produce one kilo of fish. “If we start to reuse the water, use mechanical filtration to take out the excrement, add some air – then you can reduce water consumption to around 16,000 litres. If you reduce the water even further to what we call moderate RAS systems, then we are using around 500 litres of water to produce one kilo fish – a factor of 100.”
The RAS system has other advantages, says Ewen Leslie. This hatchery grows salmon from egg up to the juvenile smolt size, then transports them out to a marine farm for on-growing.
Recirculation means you're recycling 96% of the water. Therefore, the energy you're putting into it, you're reusing it, you're not wasting it at all.
Ewen Leslie, Freshwater Engineering Manager at Scottish Sea Farms
“In the natural environment, a salmon reproduces in a freshwater river. When the fish goes to smolt and heads back down to the river mouth to go out to sea, from that egg to that smolt in the natural environment, you have a 95% mortality rate, 5% survival rate,” he says. “In a RAS production area where you control the environment, we’ve turned that around, achieving a 90% survival rate.”
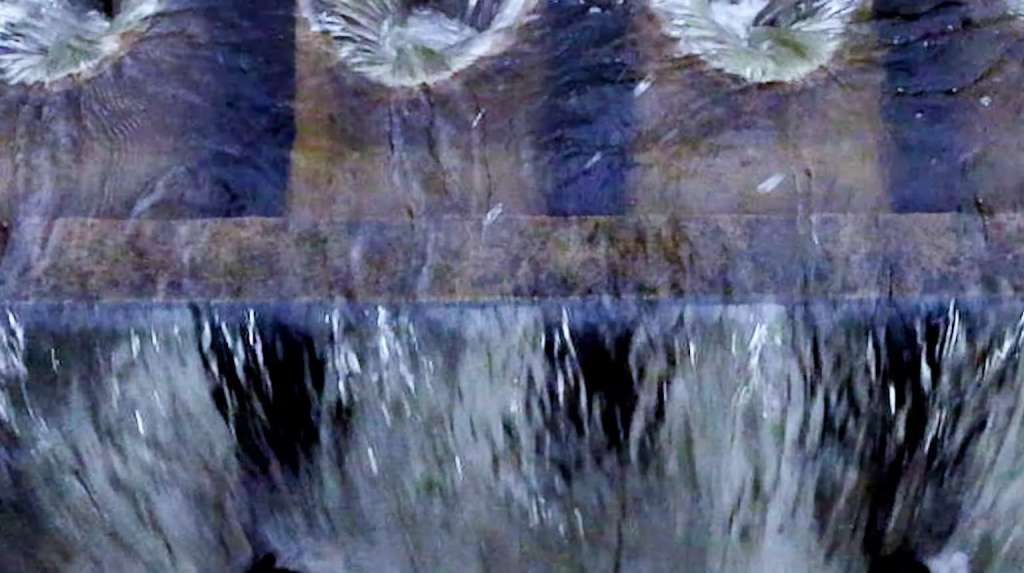
The hatchery reuses 96% of the water and can carefully control temperature, pH, salinity, feed amounts and so on.
The solution
Around the time the company was planning a new hatchery in Barcaldine in the Scottish Highlands in the mid-2010s, a new technology had matured, called recirculating aquaculture system [RAS].
“Recirculation means you’re recycling 96% of the water,” Ewen Leslie says. “Therefore, the energy you’re putting into it, you’re reusing it, you’re not wasting it at all.”
Billund Aquaculture’s Bjarne Hald Olsen says, “When choosing the pump brand for a recirculation system, we must look into the sustainability, reliability, the maintenance and service. And there we have had Grundfos as a reliable partner since we began in 1986.”
The Barcaldine facility has more than 250 Grundfos pumps in different capacities moving water and fish around the hatchery.
“When we’re in full production, we could have up to 12 million juvenile fish from egg right through to 120-gram smolts in 12 production areas,” says Leslie. “If a pump went down on one area, we could lose as many as 1.5 million fish. So it’s very important that we have redundancy. And we have reliability, which we get from Grundfos.”
If a pump went down on one area, we could lose as many as 1.5 million fish. So it's very important that we have redundancy. And we have reliability, which we get from Grundfos.
Ewen Leslie, Freshwater Engineering Manager at Scottish Sea Farms

Each room of fish tanks has a corresponding room of pumps of various types and sizes to control the RAS system.
RAS pump applications
A few of the main pumping applications in the Barcaldine hatchery include temperature control – moving warm or cold glycol to and from heat exchangers to help keep the water temperature at a steady 12°C in all fish areas. There are also pumps needed to move water from a return sump up through the RAS system’s biofilters, back down into a trickling sump and then pressurising again through UV disinfection units. From there, the pumps move water into oxygen cones and further into the fish tanks, Leslie says.
“Grundfos pumps can deliver the same output water-wise for less current,” he says. “So our energy usage is controlled that way. We need a steady 1.6 MW to run the facility and move the fish and water about the hatchery.
So every little bit of energy we can save is a bonus to us – and reduces our carbon footprint as well. That’s another factor for choosing Grundfos pumps.”
In the beginning, Scottish Sea Farms used local pump suppliers to source the pumps and spares. “But through local contacts, I got to know one of the sales area reps for Grundfos. We had a meeting, and I got to explain the challenges we were having getting spare parts, spare pumps, the long lead times. So Grundfos then made us a Priority 2 customer, which means we can deal directly with them.
Now we have access to a much bigger pump stock. It saves us having to have a vast number of spares and stock held on site. We can now call on Grundfos to help us out and give us a quick turnaround on a pump repair, or supply of a new pump or supply of pump parts.”

Pumps in the Energy Central send warm glycol to heat exchangers to help keep fish tanks at a steady 12°C.
“ Grundfos pumps help us maintain fish survival rates, then help us achieve greater water reuse.”
Ewen Leslie, Freshwater Engineering Manager at Scottish Sea Farms
The outcome
Ewen Leslie says that RAS can help with future global food production in a more sustainable way. “Having a facility like this means that we can better mimic the natural environment of the fish, which means they are going to grow quicker, bigger, and more robust. When they go to sea, they then have a stronger chance of survival. Which means more fish at the end of the day that we can then provide to the world.
“Grundfos pumps help us maintain fish survival rates, then help us achieve greater water reuse,” he adds. “And we move it around quicker, easier. And we will know that when we switch on the pump, it’s going to run for us 24/7 for the duration that the manufacturer has specified.”
He says that since it started in 2019, the Barcaldine has had no major breakdowns. Further: “We’ve had no fish losses in the facility. And we’ve had compliments back from our marine farms that we are now producing the biggest, most robust smolts they’ve had. The smolts are also fed straightaway on day one, which has never happened before from other smolt suppliers. So that, to me is our biggest achievement.”

Pumps in the Energy Central send warm glycol to heat exchangers to help keep fish tanks at a steady 12°C.

Mark Bennett, Grundfos UK & Ireland Sales Engineer, with Ewen Leslie, Freshwater Engineering Manager at Scottish Sea Farms.
Grundfos supplied:
Case story info box:
- Topic: Recirculating aquaculture systems (RAS)
- Location: Barcaldine, Scotland, UK
- Customer: Scottish Sea Farms
Fact box on Scottish Sea Farms:
- Locations: Scottish west coast (including Barcaldine), Orkney Isles and Shetland Isles
- Freshwater hatcheries: 3
- Marine farms: 57
- Processing facilities: 3
- Barcaldine: Contains four individual hatcheries, each with its own dedicated water treatment system for the highest levels of biosecurity.
- Product: 120-gram smolt salmon for further production at marine sites
- Annual production: 12.5 million/year, resulting in 40,000 tonnes/year after full production (gutted weight, 2022)
- Performance: 90% annual average fish survival
- Customers: Premium markets, restaurants in 24 countries (50% UK, 50% rest of world); plus secondary producers
When choosing the pump brand for a recirculation system, we must look into the sustainability, reliability, the maintenance and service. And there we have had Grundfos as a reliable partner since we began in 1986.
Bjarne Hald Olsen, Chief Sales Officer, Billund Aquaculture
Our Customers Says:
“When choosing the pump brand for a recirculation system, we must look into the sustainability, reliability, the maintenance and service. And there we have had Grundfos as a reliable partner since we began in 1986.” – Bjarne Hald Olsen, Chief Sales Officer, Billund Aquaculture
Sources
The facts in this story come from interviews on site at the Scottish Sea Farms Barcaldine
Hatchery Barcaldine, Scotland, UK, and at Billund Aquaculture in Denmark on April 11-13, 2023.
More Grundfos Case Studies
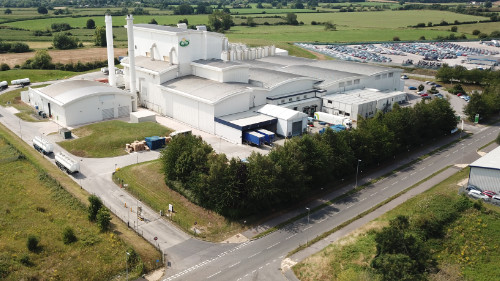
Arla achieves 481,800 kWh energy savings in critical water supply systems
Arla achieves 481,800 kWh energy savings in critical water supply systems Arla Foods, one of
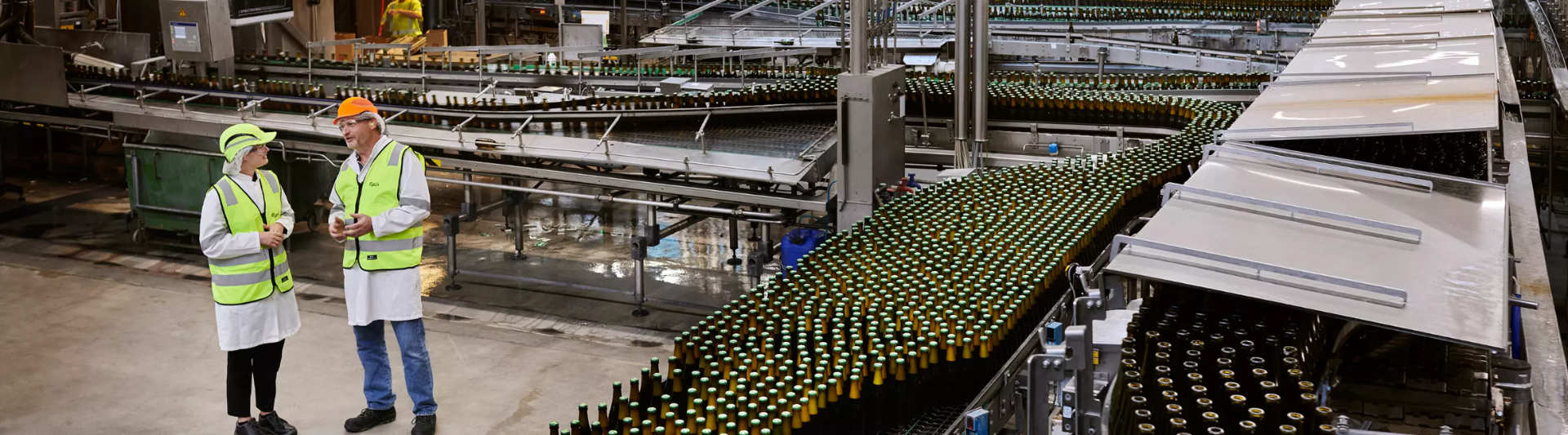
Carlsberg taps into process water reuse with onsite treatment
Carlsberg taps into process water reuse with onsite treatment Carlsberg brewery wants to cut its
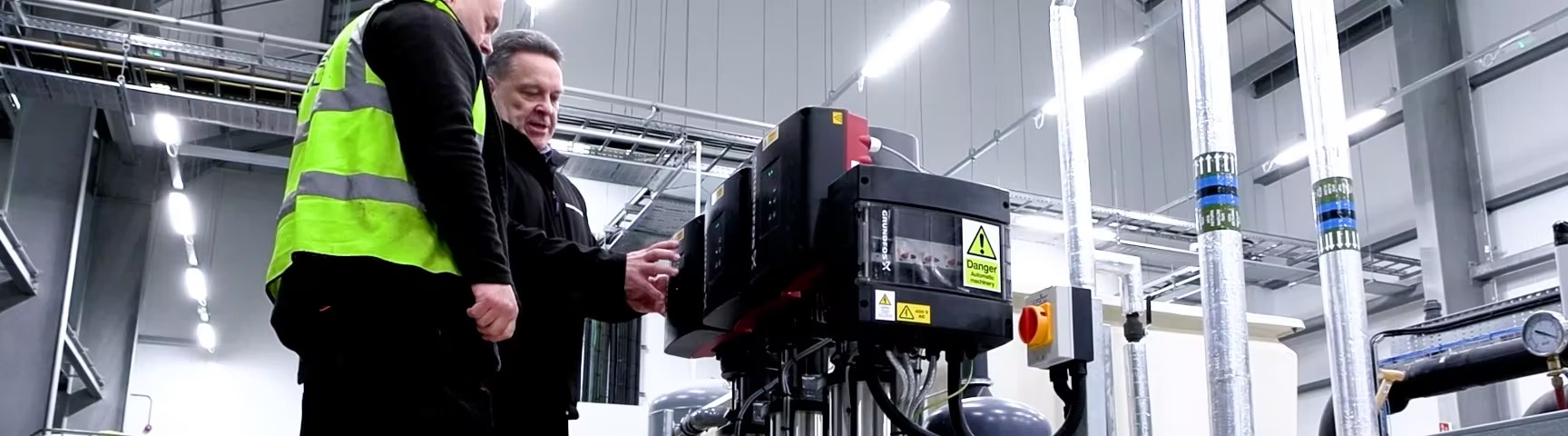
At Scottish Sea Farms salmon hatchery thrives with reliable pumps
At Scottish Sea Farms salmon hatchery thrives with reliable pumps Scottish Sea Farms wanted more
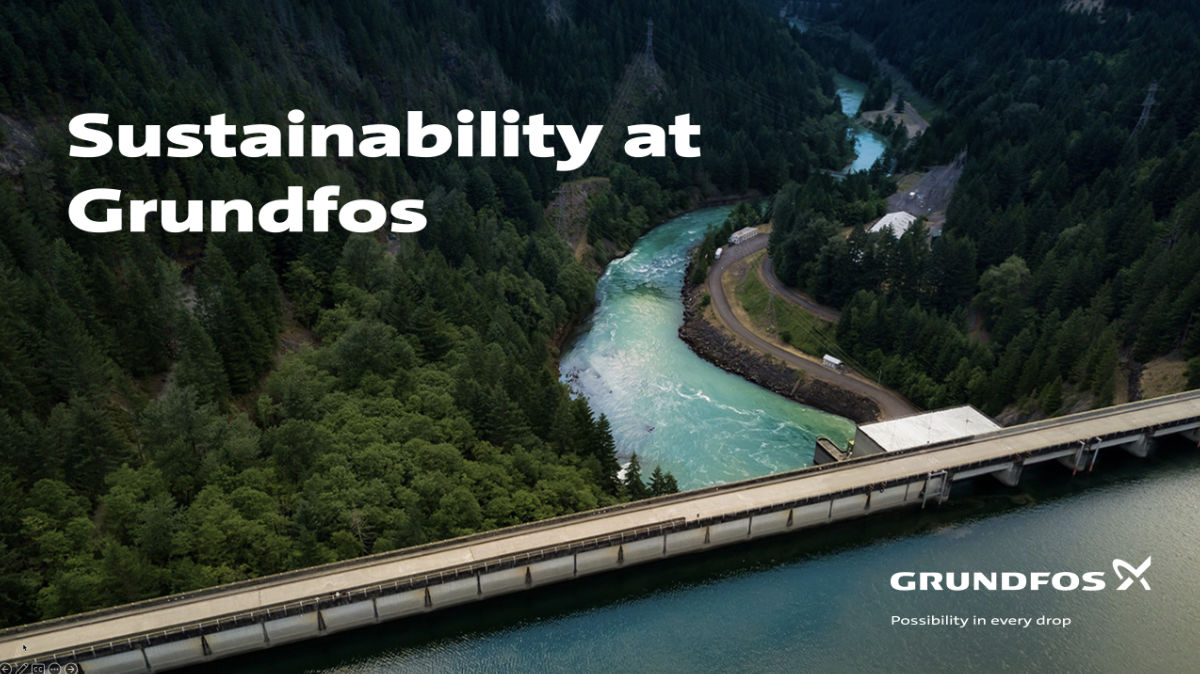
Sustainability at Grundfos
Sustainability at Grundfos At Grundfos, sustainability is at the core of everything we do and
Looking for Grundfos Pump Options?

Grundfos Domestic Range
Grundfos JP are self-priming, single-stage centrifugal pumps with stainless-steel pump housings, designed for a wide
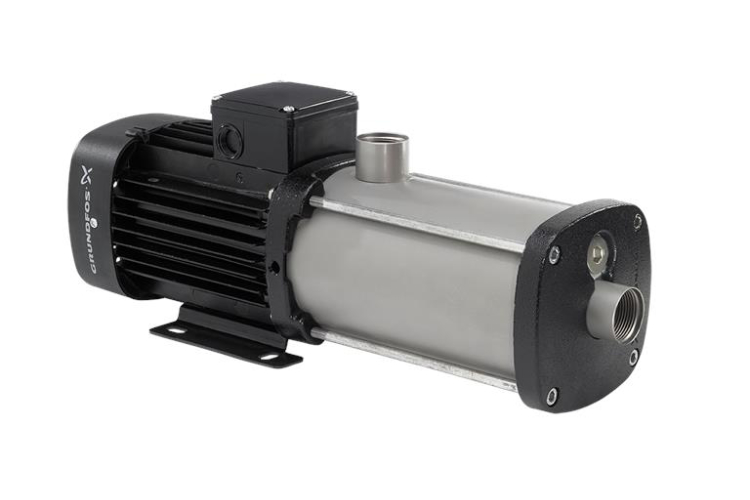
Multi Stage Pumps
In-line multi-stage pumps are used in installations in which a high head is needed. Several
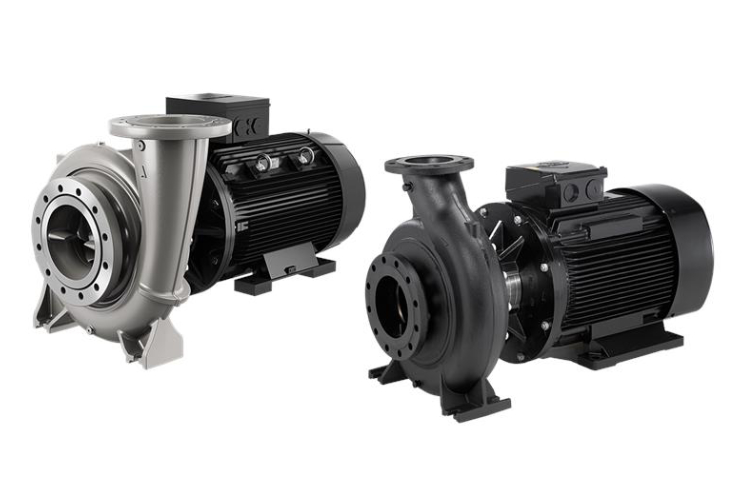
End Suction Close Coupled Single Stage
If water pressure is too high for too long, the risk of water loss, lower

Dosing Stations
MobileDos Portable dosing station Dosing is precision work and one of the main tasks in

Dosing Pumps
Grundfos SMART Digital dosing pumps and skid systems provide the reliability and precision dosing essential
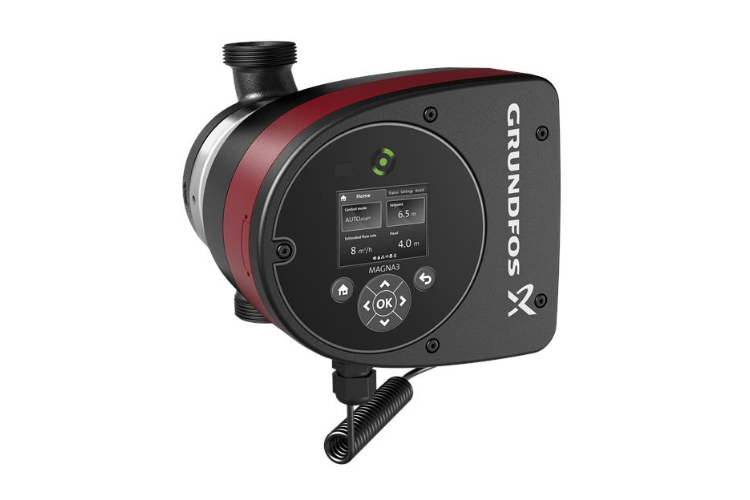
Circulator Pumps
Grundfos circulator pumps are designed for best-in-class efficiency with low maintenance. Compared to conventional circulators,

Grundfos Waste Water Submersible Pumps
Grundfos submersible wastewater pumps are designed as sealed units combining a pump and integrated motor